Автор: А.Б. Тринкер
В 2010 году в Дубае, ОАЭ был построен самый высокий в мире небоскрёб «Башня Халифа», высотой 828 метров / 5 /. Проектировало американское архитектурное бюро, строила южнокорейская фирма. Общий срок строительства с 2004 по 2010 годы. В отчёте фирмы указано: «Специально для «Бурдж-Халифа» была разработана особая марка бетона, которая выдерживает температуру до +50 °C. Бетонную смесь укладывали только ночью, в бетонную смесь добавляли лёд», «строительство Бурдж-Халифа заняло 6 лет, чтобы закончить, используя 22 миллиона человеко-часов. Были наняты более чем 30 локальных подрядчиков и 12 000 рабочих из 100 стран. Проект был действительно глобален по своей природе».
Я бы сказал – нашли чем хвастать! Интересно, что применение даже самых последних «достижений» ХХI века в технологии бетона (суперпластификаторы очередного поколения, лёд в бетонной смеси, бетонирование только ночью и только 2 раза в неделю) и логистики (миксеры, бетононасосы) не всегда гарантировало темпы (сроки) и качество бетона.
Отечественные строители имеют значительно более богатый и многосторонний опыт / 1, 2, 3, 4 / производства работ в условиях жаркого и сухого климата, при солнечной радиации и штормовых ветрах. Выбор материалов, проектирование и подборы составов любого бетона для любого климата в Мире, то есть от минус 50 градусов (например в Якутске) до плюс 55°С и при любой влажности, производят строительные лаборатории в течении 60 лет в соответствии с универсальным «Руководством по проектированию и подбору составов гидротехнического и обычного бетона» 1957 года (автор Б.Д.Тринкер), главные принципы которого: простота, доступность, ускоренная за 1-2 дня методика всех расчётов, точность результатов.
По определению, жаркий и сухой климат – при температуре выше плюс 25°С и относительной влажности менее 50%, требует многих специальных дополнительных мероприятий в технологии бетона.
В ОАЭ климат жаркий морской, но не сухой, температура достигает 50°С, но зато относительная влажность воздуха в пределах 90%, что не способствует быстрому высыханию твердеющего бетона!
Напротив, в Казахстанском Экибастузе температура в 55°С в тени, одновременно относительная влажность воздуха составляет 25-30%, что как насосом вытягивает всю влагу из твердеющего бетона! В таком климате твердеющий бетон без защиты рассыпается в прах.
В период с 1977 по 1980 годы в Казахстане на Экибастузской ГРЭС № 1 (мощностью 4 млн. квт.) были построены первые самые высотные в Азии инженерные сооружения дымовые трубы 300 и 330 метров высотой, из железобетона с проектными марками М400 (класс В30), F300 и W8 (фото 1). Основные параметры трубы – наружный диаметр у основания = 32 метра, наружный диаметр верхнего створа = 12 метров, толщина стенки изменяется от 0,8 м. у основания до 0,3 м. в верхней части. Расчётная высокая сейсмичность = 9 баллов вынудила использовать усиленную арматуру периодического профиля диаметром 38 мм, что привело к необходимости применять литую смесь с подвижностью 24-26 см осадки стандартного конуса.
В 1980 на Киришской ГРЭС в особых условиях была построена 320-метровая дымовая труба (фото 3) с единственным иностранным оборудованием – бетононасосом.
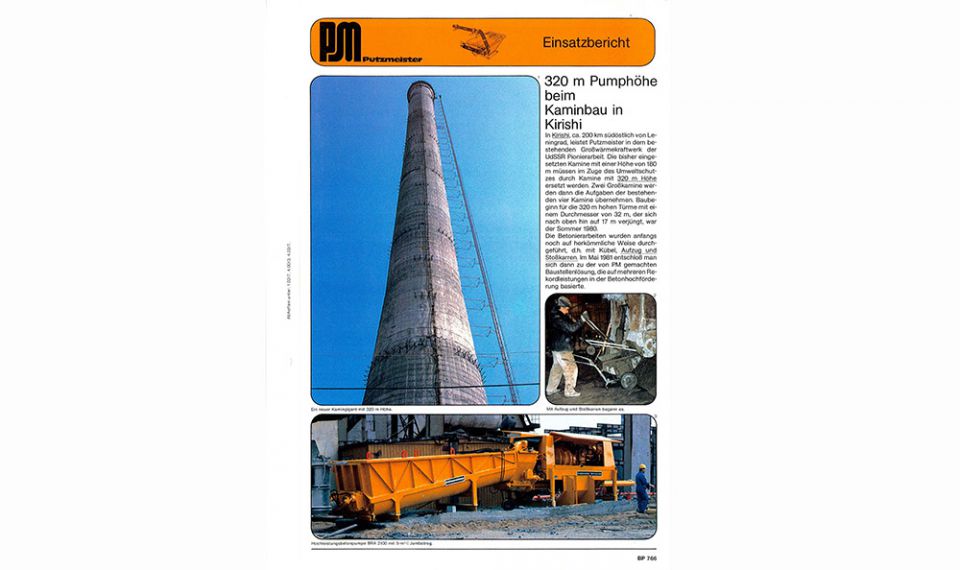
В 1985 году на Экибастузской ГРЭС № 2 была построена самая высокая в Мире дымовая труба высотой 420 метров (фото 3). Диаметр трубы у основания 44 метра, на отметке 420 м. = 14,2 метра, 35 000 м3 бетона.
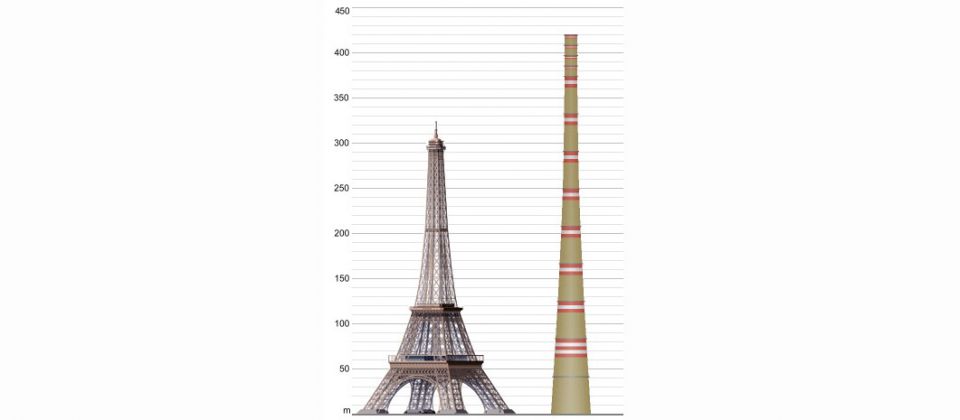
Сравнивая с «Башней Халифа» (фото 4), каждую дымовую трубу строили: генподрядчик трест Экибастузэнергострой Минэнерго СССР (владелец БСУ и складского хозяйства) и субподрядчик, трубу № 1 В.О. «Гидроспецстрой» Минэнерго СССР, а трубу № 2 трест «Спецжелезобетонстрой» Минмонтажспецстроя СССР. В бригадах было по 200 рабочих на каждой трубе, строительство каждой трубы происходило около двух лет, причём труба № 1 с последующим монтажём второго внутреннего ствола из кремнебетонных панелей, труба № 2 с одновременным бетонированием внутреннего ствола из лёгкого керамзитобетона с химдобавкой АЦФ-3М (изобретение Б.Д.Тринкера).
В отличие от жилых небоскрёбов построенных в ХХ1 веке, дымовые трубы должны долго и без ремонта работать в высокоагрессивных средах : конденсатах разных кислот, выделяющихся из продуктов сгорания топлива на ГРЭС. Бетон дымовых труб дополнительно должен быть коррозионно-стойким в высоко-агрессивных средах, то есть несравнимо с условиями службы любых небоскрёбов в жилых городах.
Резко континентальный климат Казахстана показал серьёзные проблемы в технологии бетонов. Температуры в зимний период достигали минус 40°С со штормовыми ветрами от которого падали башенные краны и стены главного корпуса, в летние месяцы температура воздуха достигала 55°С в тени, при относительной влажности воздуха 25-30% (а в Дубае-ОАЭ = 90%). Причём, в течении одних суток колебания воздуха достигали 30-40°С. Например, в июле 1978 года в 7-00 час утра, когда производственные бригады отправлялись в автобусах от городского общежития на стройку, температура воздуха была 16-20°С, в 12 час дня температура достигала 40°С, в 15 час температура достигала 55°С, потом начинался медленный спад, и в момент возвращения бригад в город в 20-00 час (12-часовые смены), температура была 30-35°С, а ночью воздух «остывал» до 16-20°С.
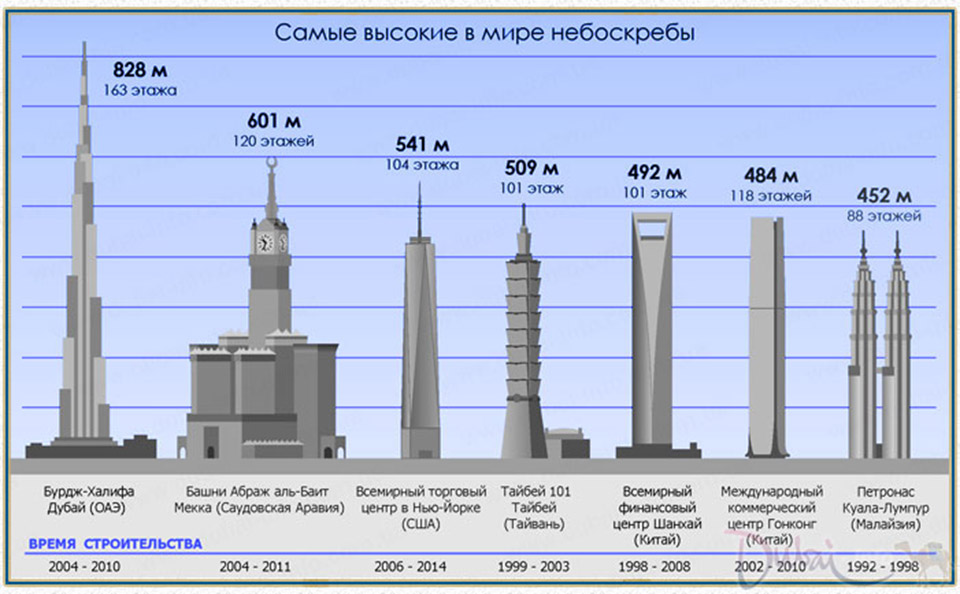
В жарком и сухом климате твердеющий бетон подвергается следующим вредным воздействиям – солнечная радиация и ветер форсируют испарение влаги из бетона сооружений имеющих большую открытую поверхность, это приводит к внутреннему массо- и теплопереносу, и к переменным термическим напряжениям в их стенках. Необходимость получения высокой подвижности литых бетонных смесей повышает расход цемента, что вызывает усадку при переменном по периметру сооружения нагреве от солнечной радиации. Трещины в бетоне сооружений возникают под влияникм усадки, от температурных и усадочных напряжений, возникающих в бетоне в процессе тепло- и массообмена с окружающей средой.
Интенсивное испарение влаги уменьшает степень гидратации цемента и приводит к образованию направленных капилляров, ухудшающих микро-и макроструктуру цементного камня и бетона, резко понижается качество бетона, его плотность, прочность, долговечность. Образование трещин и ухудшение структуры бетона под воздействием переменной по величине солнечной радиации по периметру сооружения приводят к необратимым изменениям в бетоне. Поэтому необходимо обеспечить уменьшение величины и интенсивности испарения влаги из бетона и создать все требуемые условия для полной гидратации цемента и образования оптимальной структуры цементного камня и бетона, благодаря выравниванию градиентов влажности и температуры по сечению стенок сооружения. Это достигается путём влагозащиты и теплозащиты бетона, способствующих выравниванию температуры по сечению и периметру сооружения.
Бетонирование дымовых труб Экибастузских ГРЭС происходило непрерывно и круглосуточно, дымовая труба № 1 на ЭкГРЭС № 1 возводилась в скользящей опалубке, труба № 2 ЭкГРЭС № 1 в переставной. Было практически доказано : даже в самых жёстких климатических условиях при температуре плюс 55°С и относительной влажности 30%, темпы подъёма скользящей опалубки достигали 3-4 метра в сутки, а скорость подъёма в переставной опалубке (труба № 2, ЭкГРЭС № 1) составляла 1 метр в сутки. В бетонные смеси вводили самый надёжный, простой, безопаснный в применении и успешно применяемый с 1947 года ПАВ – СДБ, который гарантированно обеспечил получение литой (24-26 см) бетонной смеси и одновременно самых высоких проектных марок бетона в сооружении: М400 (класс В30), F300, W8. Лабораторный контроль качества (мониторинг) производства бетонной смеси на БСУ, при укладке в опалубку, и последующему уходу был сразу организован непрерывно-круглосуточный.
Применение скользящей опалубки для уникального сооружения было осуществлено в СССР впервые, с целью ускорения темпов и качества, учитывая, что при переставной опалубке для сооружения высотой 330 метров, соответственно будет 330 рабочих швов в которых бетон более проницаем, а вся конструкция немонолитная. Однако, торопливость высшего начальства (П.С.Непорожний) и категорическое требование начать 12 апреля 1978 без запаса строительных материалов необходимого качества, могло привести к аварии, автор статьи был вынужден завысить марку проектируемого бетона, и кроме того строительное управление ССМУ Энерговысотспецстрой не смогло наладить непрерывный и постоянный геодезический контроль приборами PZL – в результате при темпах подъёма опалубки 3-4 метра в сутки возникли отклонения от вертикали до 600 мм. Контрольная проверка ультразвуковыми приборами показала прочность бетона выше проектной (М450 – М500) и только поэтому проектировщики согласовали окончательную высоту трубы № 1 = 300 метров, то есть завышение проектной марки бетона автором спасло дымовую трубу № 1 ЭкГРЭС № 1 в 1979 году.
Для защиты от высыхания твердеющий бетон после выхода из-под опалубки немедленно покрывали раствором водорастворимого дешёвого полимера КМЦ, который надёжно защищал бетон и обеспечивал полную гидратацию цемента до набора проектной прочности бетоном. Испытания контрольных образцов бетона, хранившихся в условиях конструкции, на прочность при сжатии, подтвердили проектные марки бетона инженерных сооружений.
Процент введения в бетонные смеси ПАВ в течении суток варьировался, дозировка ПАВ изменялась строительной лабораторией 3-4 раза в течении суток, в зависимости от изменения температуры воздуха, что обеспечило постоянное качество и подвижность бетонной смеси при укладке в опалубку с учётом потерь во времени.
Эффективно также применялись теплозащитные покрытия от солнечной радиации для выравнивания температуры по всему сечению сооружения.
Необходимо отметить: все рабочие-высотники в период строительства были обеспечены жильём, к зарплатам (основной тариф) прибавляли высотные надбавки и командировочные (вахтовый метод), не было отбоя от желающих, кроме того был коэффициент 1,3 за трудные условия, в результате средняя получка рабочего в месяц достигала 2000 рублей.
Экибастузские ГРЭС № 1 и № 2 непрерывно работают в течении 40 лет производя электрическую энергию для всего Казахстана, что доказывает высокую долговечность бетона и надёжность возведённых советскими строителями дымовых труб. Причём имеются дополнительные мощности, так как электростанции работают не в полную нагрузку, соответственно при необходимости для новых потребителей электроэнергии в Казахстане или за пределами страны, можно увеличить подключив резервные котлоагрегаты.
Опыт летнего строительства в Казахстане при критических параметрах: температуре плюс 55 градусов и относительной влажности воздуха 25-30% указывает на необходимость строгого выполнения всех требований по подготовке, приготовлению бетонной смеси и уходу за твердеющим бетоном, геодезическому контролю, что обеспечило высокую долговечность сооружений.
В результате применения простейших и надёжных отечественных технологии бетона и строительных материалов, был получен огромный экономический эффект, причём следует учесть – возведённые советскими инженерами высотные железобетонные сооружения никогда не красили (исключение – маркировочная сигнальная покраска для самолётов), а все небоскрёбы в мире защищены нержавеющим металлом, стеклом и силиконом, старые металло-конструкции, например Эйфелеву башню периодически каждые 7 – 9 лет красят.
Опыт возведения самых высоких в Азии железобетонных сооружений на Экибастузской ГРЭС № 1 в 1977-1980 годах, и самой высокой в Мире дымовой трубы на Экибастузской ГРЭС № 2 в 1985, инструкции и документы разработанные советскими учёными и инженерами, были успешно применены в ХХ1 веке при строительстве небоскрёбов (фото 4), однако надо понимать, что при всей мощнейшей западной рекламе-пропаганде, но факт : все небоскрёбы облицованы металлом и стеклом то есть защищают бетонное ядро жёсткости, Эйфелеву башню красят, а Бетон наших сооружений включая Останкинскую Царь-Башню никогда не защищали и не красили!
В 1950-1980-е годы советские строители, энергетики, монтажники успешно возводили многочисленные железобетонные сооружения во многих странах Мира, можно вспомнить знаменитые: Бхилайский металлургический завод в Индии, Асуанскую плотину в Египте, АЭС и химический комбинат на Кубе, ТЭЦ «Исфаган» в Иране, ГЭС«Хоабинь» во Вьетнаме, созданные в Китае восемь сотен заводов и комбинатов, плотины в Аргентине, в Боливии, и многие-многие другие построенные в особых условиях жаркого климата.
Чтобы уверенно направляться в будущее, надо хорошо знать своё прошлое.
Автор: Тринкер Александр Борисович, д.т.н., 25.03.1947 года рождения, с 1970 ст. инженер НИИЖБ Госстроя СССР, 1977 - 1983 Главный технолог высотных и подземных сооружений Гидроспецстроя Минэнерго СССР, 1983 – 1985 Главный специалист технического отдела всесоюзного объединения азота и оргсинтеза ГИАП Минхимпрома СССР, 1985 - 1991 Главный технолог по Новой Технике Главмоспромстройматериалов Мосстройкомитета, 1991 - 1996 Главный инженер завода ЖБИ-Лихоборы 1-го СМТ Минсредмаш СССР, c 1998 Regeneration Technology Centre & Consultung Development Innovation. Имеет несколько патентов и медалей ВДНХ СССР, более 150 опубликованных трудов с 1974 года.
_____________________________________
Библиография :
1. Тринкер, Б. Д. „Применение пластифицированного цемента и пластифицирующих добавок к бетону“, Министерство строительства предприятий машиностроения СССР, Москва - Ленинград, Стройиздат, 1952, 64 стр.
2. Тринкер, Б. Д. „Руководство по проектированию и подбору состава гидротехнического и обычного бетона», Министерство строительства РСФСР, Москва, 1957, 54 стр.
3. Тринкер А.Б. «Опыт производства бетонных работ при возведении специальных высотных сооружений в условиях сухого и жаркого климата», журнал «Специальные строительные работы», № 11, 1979, стр. 3 – 9.
4. Тринкер А.Б. «Единая система скоростного бетонирования высотных сооружений», журнал «Бетон и железобетон», № 12, 1983, стр. 20 – 21.
5. CTL Group. “Burj Khalifa, the Tallest Building in the World. ”Last modified 2011. Accessed Nov. 15, 2011.
Аннотация: в 2010 году в ОАЭ было построено самое высокое здание из железобетона в мире, а в 1979 году в Казахстане отечественные строители построили самое высокое сооружение в Азии, в таком-же жарком, но резко-континентальном климате.
Комментарии (0)